New public, private programs help train next workforce
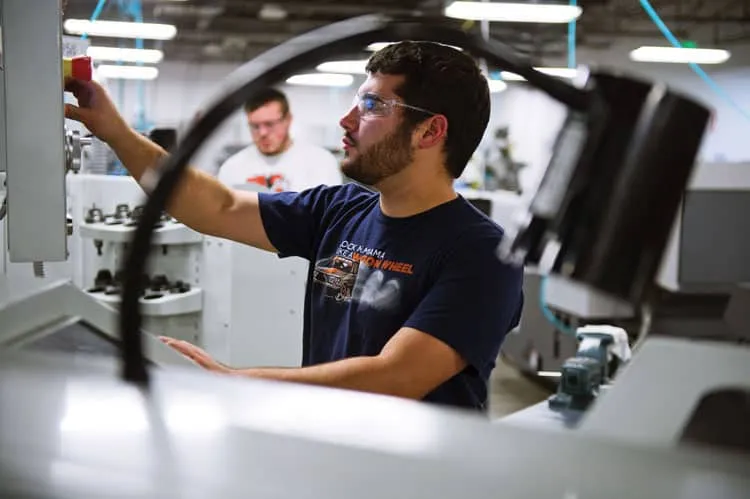
If there’s one topic on which most in business agree, it’s that there is a major skills gap in Colorado and nationwide.
The problem isn’t new, but educators and businesses in the state are working together to try and close that gap, particularly in industries that have struggled for years to fill positions.
Health care, software development and skilled trades such as plumbing, electrical and mechanical are the worst hit industries in the state.
Front Range Community College is working to address the skills gap in health care by opening a new Health Care…
THIS ARTICLE IS FOR SUBSCRIBERS ONLY
Continue reading for less than $3 per week!
Get a month of award-winning local business news, trends and insights
Access award-winning content today!