Hope Springs — seven months in
27 stick-built homes and one partially-complete 3D-printed home
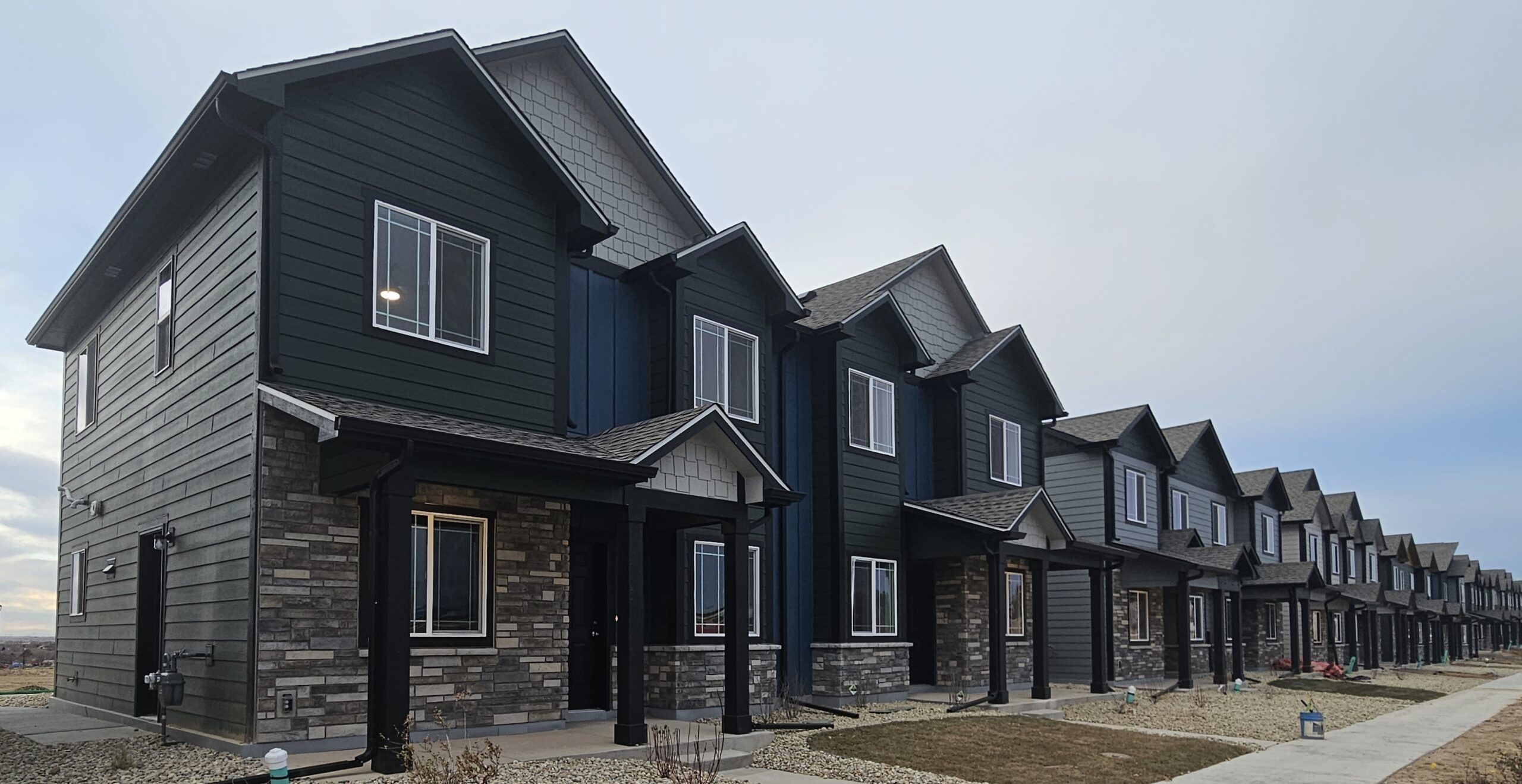
GREELEY — Seven months into the biggest Habitat housing project in her career, Cheri Witt-Brown can finally say her organization doesn’t have to turn away any families ready for home-ownership.
Witt-Brown, executive director of Greeley-Weld Habitat for Humanity, has shepherded Colorado’s largest Habitat project — Hope Springs — since its groundbreaking in June. By the time the project is complete, there will be 491 housing units, 174 of which will be Habitat homes, and 320 apartments. Today, a little more than three months after work began, 27 fully constructed Habitat homes are awaiting families, with eight more foundations already poured, and the first 3D-printed duplex in Northern Colorado almost ready to be tested.
“In our 37-year history, we’ve never been in the position where no one who has qualified for a home had to be turned away,” Witt-Brown.
SPONSORED CONTENT
Hope Springs is a collaborative effort of several organizations and individuals who together came up with $12 million to buffer the Greeley project that will allow qualified low-income residents the chance to buy a new home. The project includes single- and multi-family developments, walking and biking trails, two mini-pitch LED soccer fields, a community organic garden, a daycare center and a nature discovery park, all tucked in close to places to go to school, shop and work.
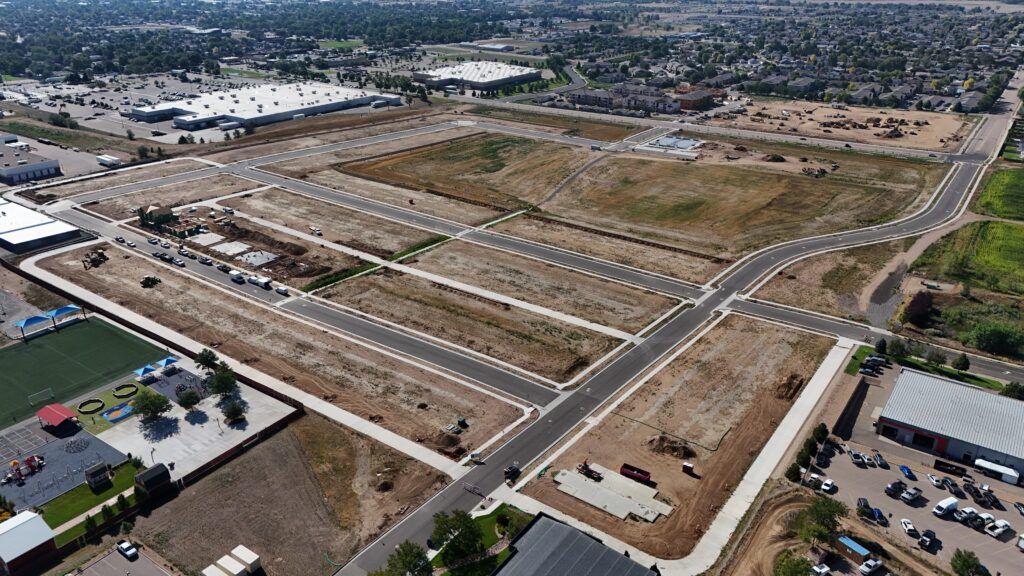
Central to the project is energy-efficient home-building. For this project, Habitat partnered with Baessler Homes, which to date has built 27 homes for the project.
“With Baessler, we have a turnkey product and can get a family in a home from start to completion in 4½ to five months (including one month for loan documents and closing),” she said. “A Habitat home built with volunteers is usually about six months. The end goal is to serve more families with well-built homes and high-quality construction. So we are able to accomplish that goal clearly with the Baessler’s product. Three and a half months is just an incredible production schedule. They have perfected a production model that is efficient without reducing quality and that’s difficult to achieve.”
Conversely, the pilot project to build the area’s first 3D printed home has taken much longer. Alquist 3D, which received $2.85 million in state and local incentives to relocate its headquarters to Greeley earlier this year, hung its hat on the pilot housing project as a potential catalyst to build more 3D homes at Hope Springs. The company had already worked with Habitat in Virginia in 2021, successfully completing three homes there. Though the company had plans to build 200 homes, they backed out of the project after the first builds, stating that the economy made the project too expensive, according to a report by WFXR TV in Virginia.
The technology and chemistry of 3D printing may still be proving itself in Colorado’s climate.
Prior to coming to Greeley, Alquist had a failed test project in Iowa, where the company planned to build 10 3D printed homes in 2022, but built only one — it was torn down a year later due to the concrete cracking under the strain of a colder environment, according to the Des Moines Register. That project also came with $3.2 million in state incentives, but much of that was for the educational component and the purchase of the 3D printer by Iowa State University, the Register reported.
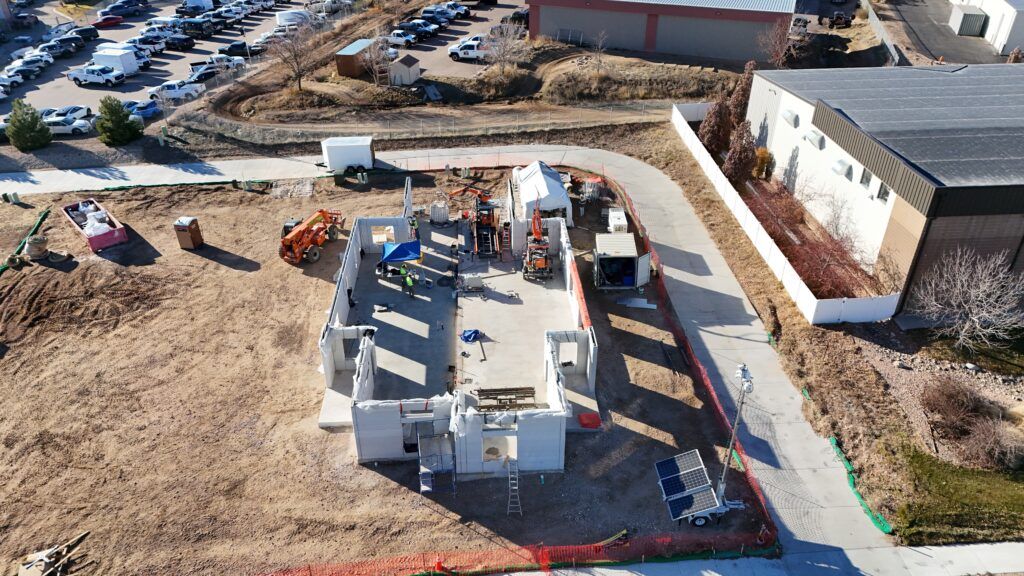
Witt-Brown said she and city officials witnessed Alquist’s 3D work in Virginia, where Alquist built three 3D homes. That was buoyed by reports of successful building of 3D printed homes from ICON in partnership with Lennar Homes in Austin, Texas. Alquist representatives also have recently built walls for Walmart in Athens, Tennessee, calling it the largest 3D-printed structure in the world.
At a recent Greeley City Council meeting, Alquist CEO Patrick Callahan said the company is now working on another Walmart. He said he understood and owned the frustration the city and Habitat has had with wanting the company to pick up the pace.
“There is a collective frustration that we haven’t gone faster,” Callahan said. “We are in the final stages, another frustrating subject, but we’re very proud of the 3,000-square-foot duplex that is roughly 94% complete. In Tennessee, it was100% and 95% humidity. We had to learn how to control temperatures. … Here, it’s different. It’s colder, so heating material was a process no one in the world knew how to do. We’re the only company in the world that built a duplex of that design, with a material that’s never been put to that limit. It took longer.”
Witt-Brown said she believes in the technology, but she also wants to test it in Colorado’s climate to see for herself. Now that the Greeley duplex is almost done, she wants to put it through the paces — to ensure it is the best product to offer any incoming family, from energy savings to quality of living inside such a home.
Witt-Brown originally had a family lined up to be the first resident of that pilot duplex in which Alquist was building only the walls. As it turned out, the family opted to get into a stick-built home in which they could put in their own “sweat-equity,” to help build their home, which is Habitat’s way of getting buy-in from their homeowners.
Billed as less expensive, quicker and cheaper to build, and more energy-efficient, this first test of a 3D-printed home is not bearing that out. The walls are expected to be complete this week, which will then open up the project for Habitat crews to build the rest — framing, windows, roofs, and flooring and finishing.
Callahan told the City Council, “Startup life is exciting; it can be difficult with a lot of achievement and failing forward.”
So far, the cost savings of 3D home printing haven’t materialized. Habitat opted to build deeper foundations for the duplex with extra rebar and concrete to ensure that the walls would be rock-steady given Colorado’s powerful winds or the potential for a tornado. The walls take the place of traditional siding and drywall. They had to put in additional insulation to ensure that the duplex could retain heat, as well.
“Both sides of the duplex, that additional cost just for the foundation ran about $40,000 per side, over and beyond our traditional concrete,” Witt-Brown said. “Our costs today are running 30%-35% higher than a traditional” build. Callahan told the council that labor is their biggest challenge.
“Seventy percent of our cost is labor,” Callahan said. “We’re trying to attack the labor side, by taking the amount of time on the station down by using automated programming.”
Witt-Brown has opted to turn one side of the duplex into construction employee housing, and the other an office and a model home, in which they can test for the next 18 months to learn how much more energy-efficient the home is, as well as gauge public interest and determine whether there is a market for the product and test quality of life.
“We’re not worried about the product structurally, but one of the things we do want to get feedback from the public is, ‘Do you like the aesthetics of this 3D-printed home?’ One of the improvements that Alquist is working on is to have more consistency with their prints. … It’s almost like stucco, which is never going to be completely consistent, but we know it adds a layer of energy efficiency. These are all the things we want to research and analyze and get feedback on.”
Having employees onsite 24/7 also will help provide necessary security, as large construction projects are usually targets of theft. In recent years, Habitat crews lost all of their tools on a construction project and had to start from scratch.
As a part of the build, Alquist is required to have one more phase of construction, which is printing the gable wall section from their warehouse, and installing it. Witt-Brown said she is hoping the duplex will be fully complete in six weeks.
Seven months into the biggest Habitat housing project in her career, the organization doesn’t have to turn away any families ready for home-ownership.
THIS ARTICLE IS FOR SUBSCRIBERS ONLY
Continue reading for less than $3 per week!
Get a month of award-winning local business news, trends and insights
Access award-winning content today!